Thailand has been touted as one of Asia’s key manufacturing center for electronics, automotive and machinery. According to the Board of Investment of Thailand, electronic components and equipment are the country’s top export category, which reached USD 31 billion in 2020. The country currently ranks 13th globally as a base for electronic products and parts manufacturing.
The COVID-19 pandemic has fuelled an increase in the demand for electronics globally, and companies in Thailand are ramping up resources and production of parts and components while ensuring resilience in the supply chain.
One of these companies is Toshiba Semiconductor (Thailand) Co., Ltd. (TST) – an important contributor to Toshiba’s network of companies which provide a robust supply of discrete semiconductors. Discrete semiconductors are ubiquitous in our daily lives, used in almost every modern device, from smartphones to automobiles and discrete components usually perform only a single function. Toshiba provides discrete semiconductors mainly in three categories: small signal devices, opto devices and power devices. Established in October 1990, TST carries out back-end processes, namely assembly and testing, of small signal devices and opto devices.
Semiconductors as a Backbone of the Digital Economy
Located about 140km north-east of Bangkok in Prachinburi Province, Toshiba Semiconductor (Thailand) Co., Ltd. (TST)’s supply of small signal devices and opto devices, especially photocouplers, are small yet vital components to drive economies in an increasingly connected world of digital century.
Toshiba is one of the world leader in discrete semiconductor business. Toshiba Semiconductor (Thailand) Co., Ltd. offers world class facilities for discrete semiconductor manufacturing.
Toshiba generally refers small signal devices as transistors and diodes with a power dissipation of one watt or less. These small signal devices control small currents and voltage in a wide variety of equipment including smartphones, computers and air conditioning units and in cars. They are essential for electrical amplification, switching, and energy conversion. The growing demand for electronic equipment and devices in end-user industries results in TST’s increasing production of small signal devices.
Toshiba Semiconductor (Thailand) Co., Ltd. offers photocouplers which demonstrate excellent performance in optical signal isolation between circuits.
Photocouplers are a type of opto devices. A photocoupler consists of a light-emitting diode (LED) and a photodetector, and uses flashes of light to transmit signal between two isolated chips. This photocoupler is often used as a switching device to transmit pulse signals between high-voltage and low voltage systems, and also used in a feedback control loop of switching regulators to prevent electrical surges and noise. It is critical as a safety mechanism especially in industrial electronic equipment which operates on factory floors and automobiles subjected to electrical surges, transient and high noise.
The back-end process of small-sized devices requires a very high precision and throughput. TST carries out the production with advanced manufacturing technologies and control systems applied throughout the entire process. This is backed by a sophisticated IT system that enables automatic data collection, fast analysis and response to maintain high quality standards. The data monitoring system detects abnormalities and allows immediate correction.
What Sets Toshiba Apart
Despite a massive flood in 2011, TST turned the crisis into an opportunity to reconsider its investment with state-of-the-art production lines. Moving the manufacturing facility to its present larger location in 2013, TST updated the production line layout to maximize production volume. This investment in the production process, known as High Efficiency Process, increases the efficiency of production, reduces wastage of raw materials and applies digital technology to control the production process. Also, the company has since been certified for quality management system standards, both ISO 9001: 2015 system and IATF 16949: 2016 system to support customers including Thailand’s automotive industry.
While the COVID-19 presented challenges in transportation, securing raw materials and onsite manpower restrictions in the industry, TST worked closely with subcontractors to ensure minimal disruptions to their production process by accelerating investment for capacity expansion, improve quality and efficiency of the production line to achieve maximum production capacity. In promoting innovation, TST is supporting in the development of products after design and pilot production have been done in Japan.
In the VUCA (Volatility, Uncertainty, Complexity and Ambiguity) era, it is important to increase manufacturing resilience. It is also necessary to deepen cooperation with related companies in its value chain. Its ability is most demanded in crisis such as natural disasters and infectious pandemics, and TST has demonstrated its strength and improved its ability to the next stage. TST continues to be an essential part of value creation to promote a digital economy.
In addition to the production of small signal and opto devices that TST has been working on for over 30 years, power devices, which play a critical role in energy-saving, have been transferred to TST to meet the rising demands of these products. Toshiba Electronic Devices & Storage Corp. (TDSC), TST’s parent company in Japan, has been diligently working to expedite the expansion of its production in both front-end and back-end process, and the company invested in both its 300 mm wafer fabrication at Kaga Toshiba Electronics Corporation, Ishikawa, Japan and assembly lines in TST. TST played an important role to support the smooth line expansion with minimal lead time. During the COVID-19 pandemic, the company’s highly skilled engineers in Thailand could successfully set up new lines without onsite support from Japan. Also, the team worked closely with TDSC for technology transfer of these power devices remotely during this challenging period.
As Toshiba’s largest semiconductor back-end manufacturing facility, TST is expected to be a core base in Asia Pacific with the introduction of products such as power devices through investments, which are used in a wide range of applications such as consumer electronics, automobiles, and industrial equipment.
Committed to People. Committed to the Future.
The company believes strongly that people are the most valuable asset. A 1,000 strong local workforce goes through continuous training and compete annually with other employees in group-wide technical competitions to boost local capabilities that support large-scale back-end manufacturing. TST also promotes a decentralized organizational structure which respects practical work decisions focused on empowering employees to make the right decisions. TST has also been awarding scholarships to unversity students, who have been selected to study in Thailand and Japan, to raise the local capabilities in engineering and industrial science.
TST is committed to be environmentally conscious in its manufacturing processes and facilities. TST has participated in energy-saving projects by monitoring and controlling energy consumption daily. Along with the emphasis on the design of the factory according to the Eco Factory principle, TST has installed energy-saving LED lamps in the entire manufacturing facility and is designed to allow natural light in the production area.
TST President Mr. Masahiro Ogushi remarks, “Toshiba Semiconductor (Thailand) is well-positioned to support the global demand of discrete semiconductors. With strong government support, modern infrastructure with efficient production capabilities and world-class connectivity backed by a skilled workforce to support Thailand’s vibrant electronics industry, TST remains committed to be a strategic production base for Toshiba’s network of companies to support the digitalization of today and the future.”
Source: Neo Target
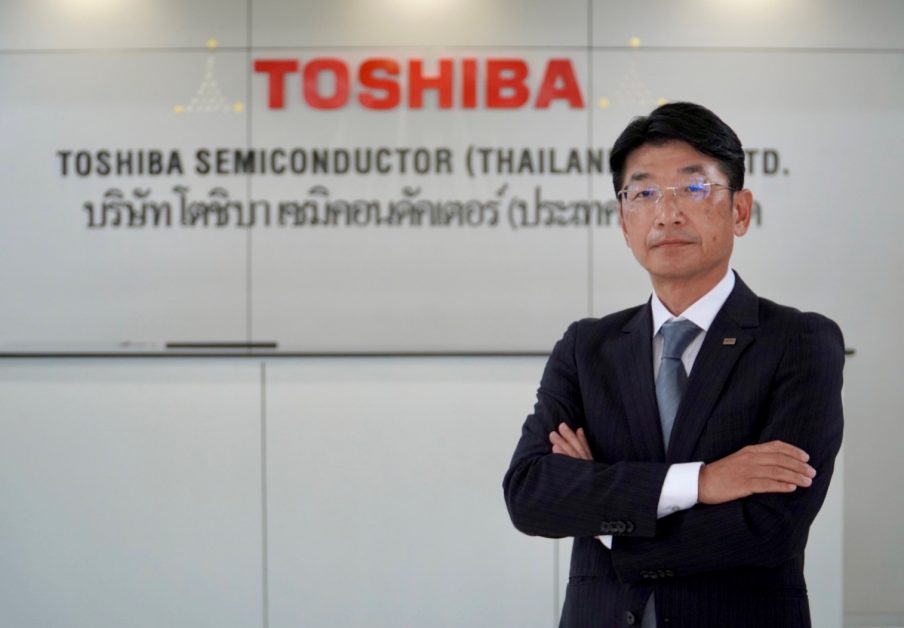