Fujitsu Limited today announced the development and deployment of a factory-wide production status visualization system in cooperation with Ricoh Co., Ltd. Ricoh has started full-scale operations of the system in June 2021 at its Numazu Plant, which manufactures polymerized toner (1).
The new system leverages Fujitsu’s plant visualization solution, FUJITSU Manufacturing Industry Solution COLMINA Intelligent Dashboard (2), to collect and process production information from Ricoh’s chemical plant in Numazu, Japan, offering a comprehensive view of the entire plant’s production status in real-time. Connecting the system with smartphones, tablets, and other devices makes it possible to visualize the status of plant operations and changes in product quality anytime and anywhere, empowering management with the ability to remotely manage factories and quickly intervene to prevent potential disruptions to smooth operations, including facility anomalies and quality defects.
Going forward, Fujitsu will play an active role in supporting Ricoh’s plans to expand the system to other locations and will continue to support digital transformation (DX) initiatives at its various production sites.
Background
Ricoh’s Numazu Office serves as its base for research, development, and production of chemical products. The office carries out R&D and production of image forming supplies such as polymerized toner and ink, thermal products (3), and new business development for areas including next-generation solar cells and new materials. At the chemical plant, a large-scale facility producing polymerized toner, products flow through tanks, pipes, and processing equipment and the condition of the products cannot be confirmed from the outside. Instead, product condition is determined through information from facility sensors and sampling inspections. To enable a small number of on-site workers to safely manage and respond to information drawn from a massive number of facility sensors, it’s imperative to provide operation status reports from the plant quickly and intuitively to field workers to ensure safe operations and quality assurance. With COVID-19 preventing site managers from visiting sites at times, Ricoh has also been exploring new working styles for the “New Normal”.
Under these circumstances, Ricoh and Fujitsu embarked on the joint development and deployment of a system for visualizing the entire plant’s production status in September 2020, which supports speedy and safe remote plant management, guided by the chemical plant’s theme of “Helping People Work Smarter”
Overview of the Factory-Wide Production Status Visualization System
The new system realizes quick and intuitive management of the safety and quality status of the chemical plant in near real-time using Fujitsu’s factory visualization solution, COLMINA Intelligent Dashboard, processing, accumulating, and visualizing data for indicators to be managed, including operation information and logs, drawing from an enormous amount of data from sensors and production equipment in the plant.
By connecting the system with smartphones and tablets, it is possible to visualize the operation status and changes in product quality at the factory anytime and anywhere even when the site manager cannot physically visit the production site. The system allows managers to work remotely to respond quickly to prevent disruptions to production and quality defects by making data-driven decisions and giving effective instructions to workers in the field.
Future Plans
Ricoh’s Numazu Plant will focus on higher-value-added operations by utilizing the factory-wide production status visualization system to reduce the administrative burden on site managers and workers. Ricoh is also planning to implement this system for visualizing the overall production status of plants to other locations as well.
Fujitsu will continue to support DX initiatives at Ricoh’s production sites, while promoting DX, enhanced competitiveness, and contributions to the attainment of sustainability targets including the SDGs throughout the manufacturing industry as a whole, in keeping with its mission for its manufacturing brand, COLMINA: “Bringing innovation to manufacturing through the delivery of services that are global, open, and rapid that help to realize DX”.
[1] Polymerized toner: High-performance toner used in printers and other applications that delivers clear images and superior print quality.
[2] FUJITSU Manufacturing Industry Solution COLMINA Intelligent Dashboard: Collects and visualizes production equipment operation data and production data, enabling users to grasp the production status of the entire factory. By utilizing cloud services, it is possible to compare global locations.
[3] Thermal products: Products and devices that display text, images, etc. by heat.
Source: 360 Degrees Media Co.,LTD
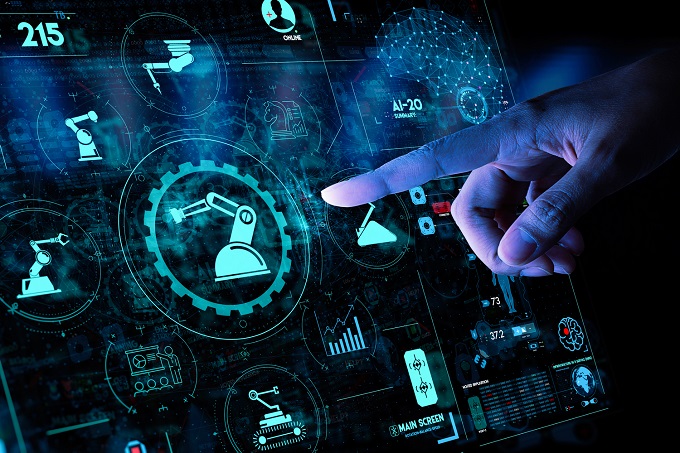